Optimising Materials Handling for Scalable Mining Operations
- Mining Plus
- Mar 10
- 2 min read
At Mining Plus, we are committed to providing innovative solutions that drive efficiency, sustainability, and scalability for our clients. A prime example of this is the trade-off and value engineering study we conducted for an underground mine in the Philippines. This study focused on optimising materials handling methods to support deeper mining levels and increased production. By exploring both traditional and cutting-edge green technologies, we were able to provide our client with actionable recommendations that aligned with their pre-feasibility goals and operational scale-up plans.
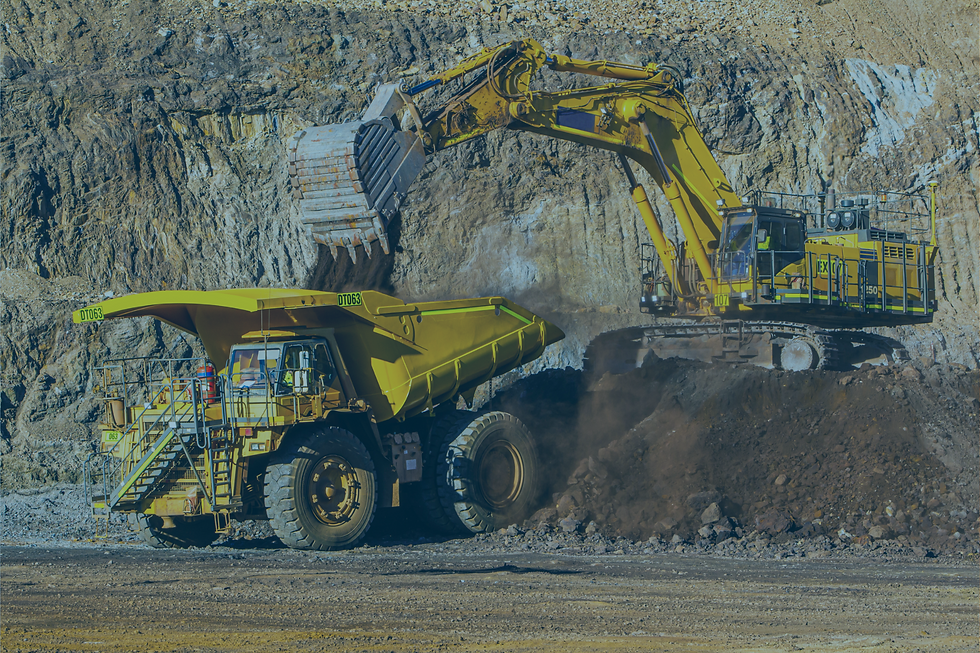
Challenges
The client faced multiple obstacles when trying to find the most effective materials handling solution for their high-production, deep-mining operation. The key challenges included balancing capital costs, operational expenses, and environmental impact, all while ensuring the solution was compatible with existing infrastructure. Traditional methods, such as conveyor and shaft haulage, required significant upfront investment, while newer technologies like Battery Electric Vehicles (BEVs) and Diesel-Electric Hybrid trucks introduced concerns around reliability, maintenance, and availability in the market.
Furthermore, the client needed a solution that could not only meet current production demands but also accommodate future technological advancements. The ability to remain flexible and scalable was essential to ensure ongoing operational success.
Our Solutions
Mining Plus took a systematic approach to evaluate five materials handling methods: Diesel Trucking (Base Case), Conveyor, Shaft Haulage, BEV trucks/loaders, and Diesel-Electric Hybrid trucks/loaders. Each option was assessed based on a variety of factors, including cost implications, infrastructure requirements, environmental impact, and its alignment with the client’s long-term production targets.
We completed comprehensive financial modelling and basic designs for the conveyor and shaft methods to accurately gauge capital and operational costs. We also partnered with Byrnecut’s electrification experts to assess the feasibility of hybrid diesel-electric technology. Using scenario modelling, we were able to provide the client with comparative insights into each method’s potential benefits and limitations.

Outcomes
Based on our findings, we recommended an expanded diesel trucking and loading fleet as the most cost-effective and flexible solution for meeting the client’s immediate production goals. Diesel trucking offered the lowest capital outlay, established performance, and the adaptability needed for future upgrades. While the Diesel-Electric Hybrid fleet showed potential as a greener option, its prototype status and related uncertainties limited its viability for the current phase of the operation.
The shaft and conveyor systems, while effective for large-scale operations, required higher initial investments and offered less flexibility, which made them less suitable for the client’s near-term production needs. Our recommendations allowed the client to make a financially sound decision that also preserved the opportunity to incorporate greener technologies as they become commercially viable.
At Mining Plus, we understand the importance of selecting the right materials handling method for scalable mining operations.
By carefully evaluating different options and balancing capital costs with operational flexibility, we were able to provide our client with a solution that supported both their immediate and long-term goals. Our approach enabled them to scale operations efficiently, cost-effectively, and with a vision toward future sustainability.
As the mining industry continues to evolve, we remain committed to offering forward-thinking, tailored solutions that support the growth and success of our clients.
Comments